航空宇宙関連部品の加工を手掛ける株式会社エヌエス機器は、1983年にNS化学工業所として創業した、研磨加工を得意とする石巻の企業です。創業当時は、自動車用組立電線(ワイヤーハーネス)や携帯電話のアンテナの組み立て、電子機器筐体のバリ取りや磨き加工を行っていました。その後、あることをきっかけに研磨加工分野に本格的に参入し、現在では、H3ロケットに搭載されているメインエンジン「LE-9」の部品加工やボーイング787のエンジン部品を手掛けるまで事業を拡大しました。
今回は、代表取締役の阿部氏、取締役で工場長の津田氏、製造部部長の高橋氏、製造技術・業務課リーダーの沼倉氏に、同社の事業内容や産業技術総合センター(以下「センター」)の活用事例、AM※1分野における研磨加工技術の研究などについてお話しをお伺いました。
また、インタビューの後半では、国内でも特筆した技術力を持つ同社を支える若手社員三名にも業務の内容をお話しして頂きました。
※1 AM:Additive Manufacturingの略。特に産業用途向けの3Dプリンター技術を指すことが多い。
複雑な部品の「理論」に基づいた研磨加工
「ハーレーダビッドソンのブレーキレバーやクラッチレバーの磨きの仕事をはじめたのが、研磨加工事業に本格的に参入するきっかけです。その後、亜鉛ダイカスト製のデジカメの筐体や、ステンレス製の半導体関連部品の研磨加工も手掛けました。」(阿部氏)
過去に電子機器筐体の研磨加工に携わった経験を活かして、オートバイクの部品の研磨の仕事を引き受けたことを機に、この分野に力を入れ始めた同社は、その技術力の高さから徐々に市場を拡大していきます。
「自動化が難しい複雑な形状の部品を磨くのが得意です。面粗度など、顧客の要求スペックに応える技術を持っています。」(津田氏)
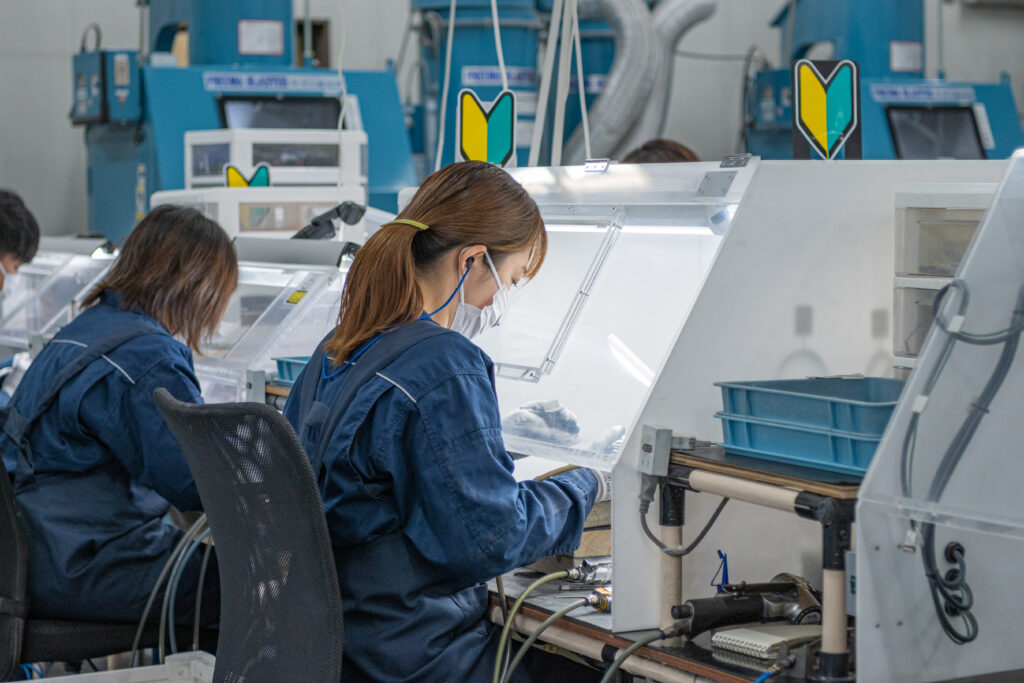
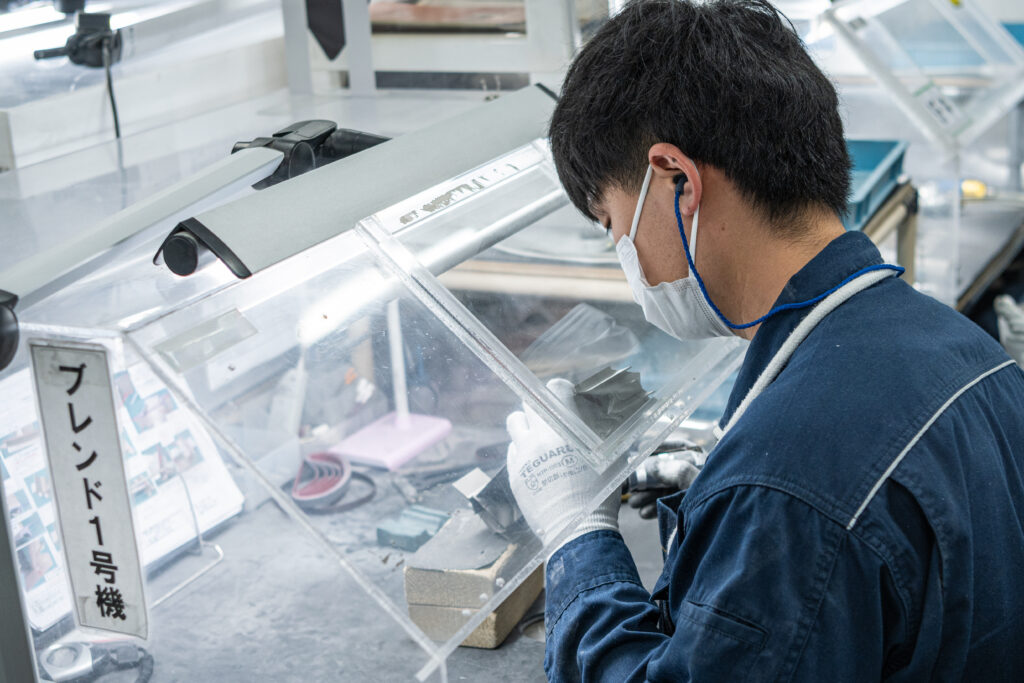
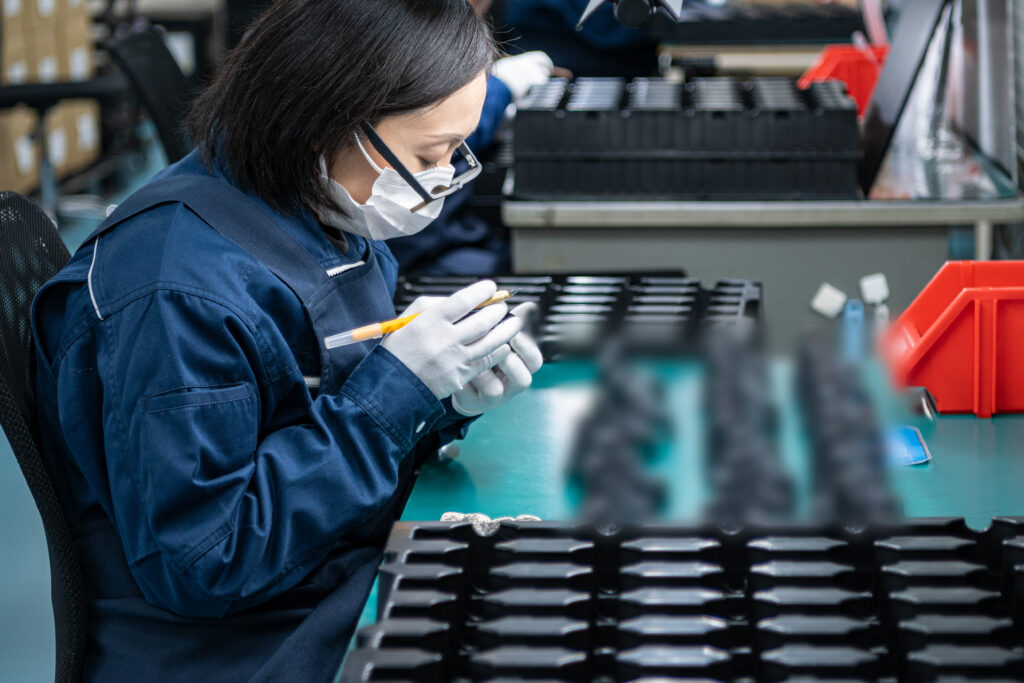
「みやぎ産業振興機構と仙台市の産業振興事業団の方の紹介で、東北大学金属材料研究所の千葉晶彦教授(現・東北大学未来科学技術共同研究センター特任教授)の依頼を受けたことがあります。コバルト系の合金製の人工関節で、3Dプリンターで作られたものを磨いて欲しいという依頼でした。千葉先生からは面粗度Ra※210nm以下にしてほしいと言われたんですが、面粗度なんて今まで考えたことがなくて(笑)、センターに何度も計測に行ったんです。それまでの研磨加工の分野は、“光ってればいい”とか、“線(ヘアライン。磨いた時にできる細かい線状の傷のこと)が一方向にそろってればいい”という仕事だったので。」(阿部氏)
金属材料の専門家である千葉教授の依頼を受け、同社の技術者は研磨加工の実験と面粗度の計測を繰り返し、最終的に面粗度Ra7nm以下を実現しました。この依頼がヒントとなり、実際の計測値を基に理論的に研磨加工を行うことが、今までの家内工場的な加工方法との差別化となると考えた同社は、自社でも表面粗さ測定機を導入し、技術力をさらに高めていきます。
※2 面粗度Ra:物体表面の微小な凹凸を平均値として表した数値。面粗度は物体表面の微小な凹凸の度合いのことで、Ra(算術平均粗さ)は面粗度を表す数値の一つ。一般的にRaが200nmを下回ると鏡面仕上げと呼ばれる
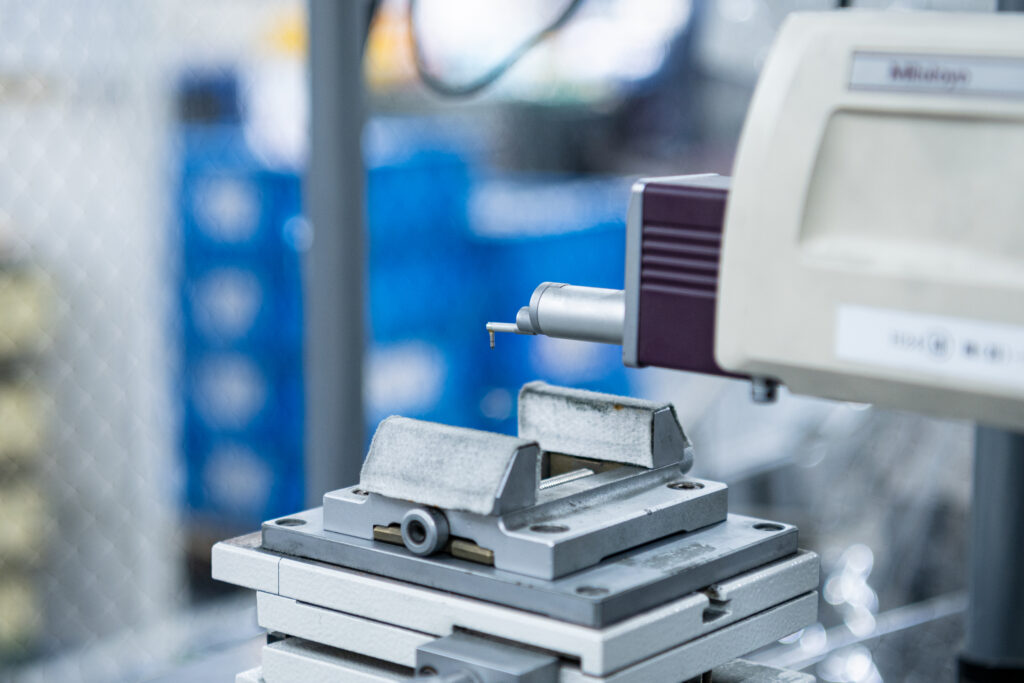
H3ロケットの打ち上げ成功を支えた技術力
「旅客機ボーイング787に搭載されているゼネラル・エレクトリック社製のTF34というエンジンに使われているタービンブレードや、戦闘機のアフターバーナー(ジェットエンジンの推力を上げる装置)の部品の加工も手掛けてきました。研磨すると摩擦熱がでますよね?航空機の部品には、加工時に発生する熱の影響による組成変化を起こさないことが求められるんです。加工後の組成変化の様子を調べるために、(株)IHIエアロマニュファクチャリングの方に協力してもらい、チタン製のサンプルピースで加工条件を変えて何度も実験を行いました。」(阿部氏)
「そんな私たちの姿勢を評価してくれたんだと思います。(株)IHIキャスティングスのロケット部門を紹介してもらって、そこから宇宙分野の部品加工に携わりはじめました。H-IIロケットのLE-7というエンジンに使われているターボポンプの部品です。今はH3ロケットのLE-9エンジンの部品加工を行っています。H3ロケットの打ち上げの時は、(何度も打ち上げに成功した実績がある)H-IIロケットの時よりも、ものすごく緊張しました。」(津田氏)
「ロケットエンジンの部品を何百個も磨いて納品するんですが、最終的に使われるのはその中の本当に優等生のものだけでしょうね。アンモナイトみたいな形状の部品や、60枚くらいの小さなファンがついた部品を磨くんです。JAXAの方をはじめ、ロケット開発に携わる方々の努力は並大抵じゃないはず。そういった人たちの努力が報われるように、自分たちも負けないくらい頑張ろうと思っています。」(高橋氏)
H3ロケットの打ち上げ時は社員みんなでテレビを囲んでその行く末を見守り、打ち上げの成功が分かると社内は大きな拍手とたくさんの笑顔で包まれたそうです。
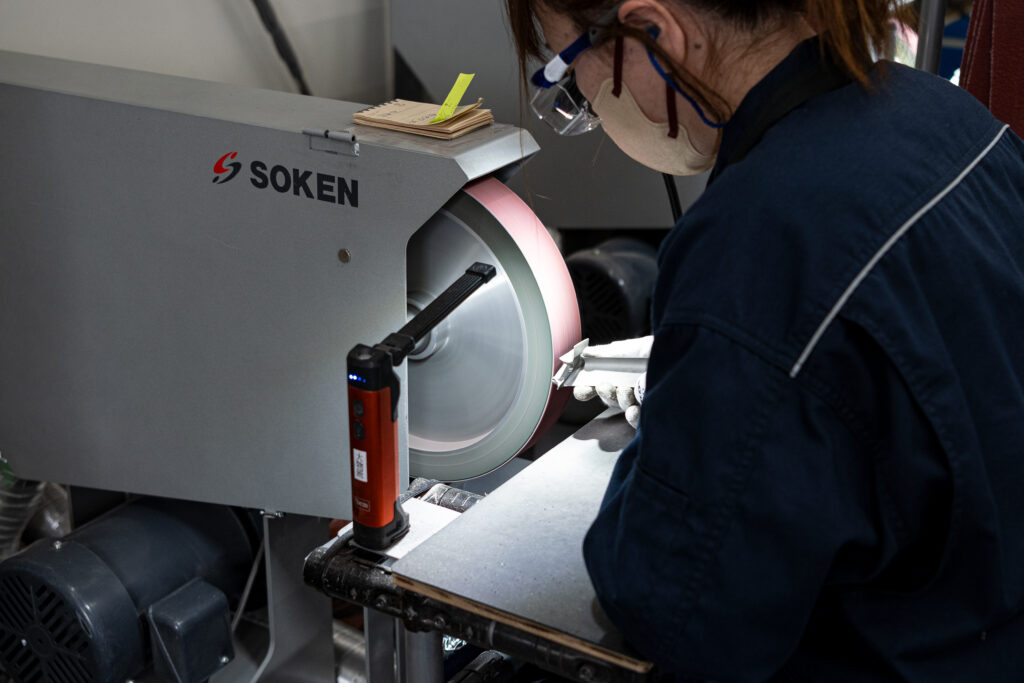
3Dプリンターや3Dスキャナーを活用して量産工程で使う治具を開発
「センターと協力して行った研磨加工用の治具の開発では、最終的に、78分かかっていた工程を63分まで短縮できました。治具の開発コストも、加工時間が短縮したことにより約一ヶ月で回収できています。」(沼倉氏)
センターでは同社からの依頼を受け、共同で金属部品の量産工程で使われる治具の開発を行いました。まずは現状の作業工程を調査して作業の課題を抽出し、治具の設計指針を話し合いました。設計指針が決まると、アーム式デジタイザ(産業用3Dスキャナー)を用いて金属部品の3Dデータを取得し、3D-CADを使って金属部品の形状に沿うように治具を設計していきます。設計した治具は3Dプリンターで造形し、現場でテストすることを繰り返しました。作業者の声を聞きながら設計変更を重ね、最終的な治具が完成しました(下記図)。
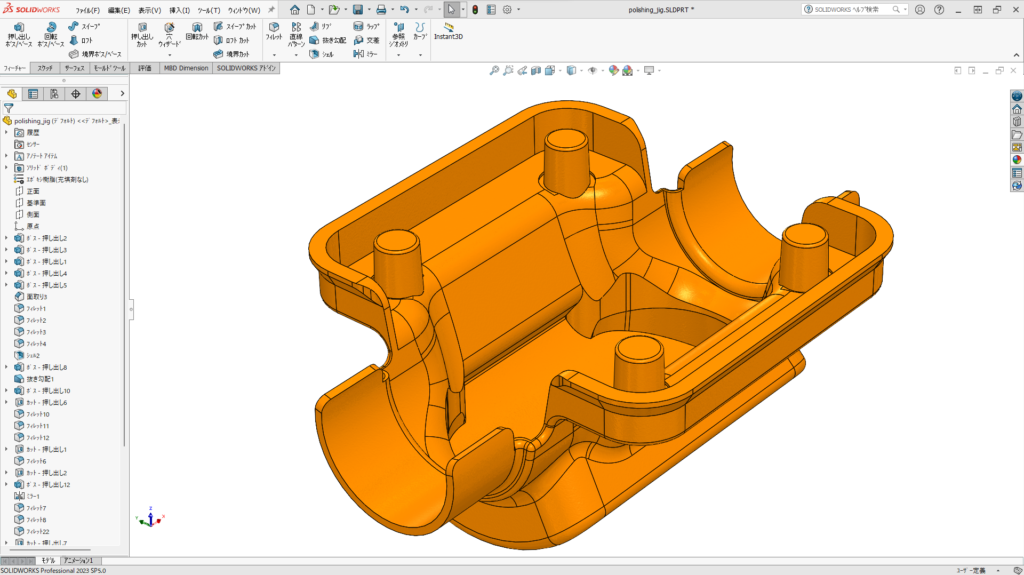
「初期モデルは寸法精度の高い光造形を使ったのですが強度が足らず、熱溶解積層タイプの造形機に変更しました。材料は、熱で色が変わる特殊なPLA(ポリ乳酸)樹脂を使っています。磨いた箇所周辺の治具の色が摩擦熱で変化するので、作業の大まかな目安になります。特に、まだ慣れていない作業者を指導するとき、未加工の部分が可視化されるので指示を出しやすいんです。」(沼倉氏)
開発した治具の形状は持ちやすく、且つ金属部品の形状と同心円状に設計されたグリップが特徴で、作業時の手ブレを最小限に抑える効果があります。また、磨いてはいけない箇所を覆い隠す形状や、研磨剤が部品内部に侵入しないようにするためのストッパーがついていたり、様々な工夫が盛り込まれています。これにより、作業者による品質のバラつきが安定し、研磨後の洗浄作業(残った研磨剤や研磨くずの除去作業)にかけていた時間もぐっと短くできたそうです。
「3Dプリンターや3Dスキャナーの技術とアイデアがあれば、まだまだ改善できる工程があると思います。これからもいろいろなアイデアを考えていきたいです。」(沼倉氏)
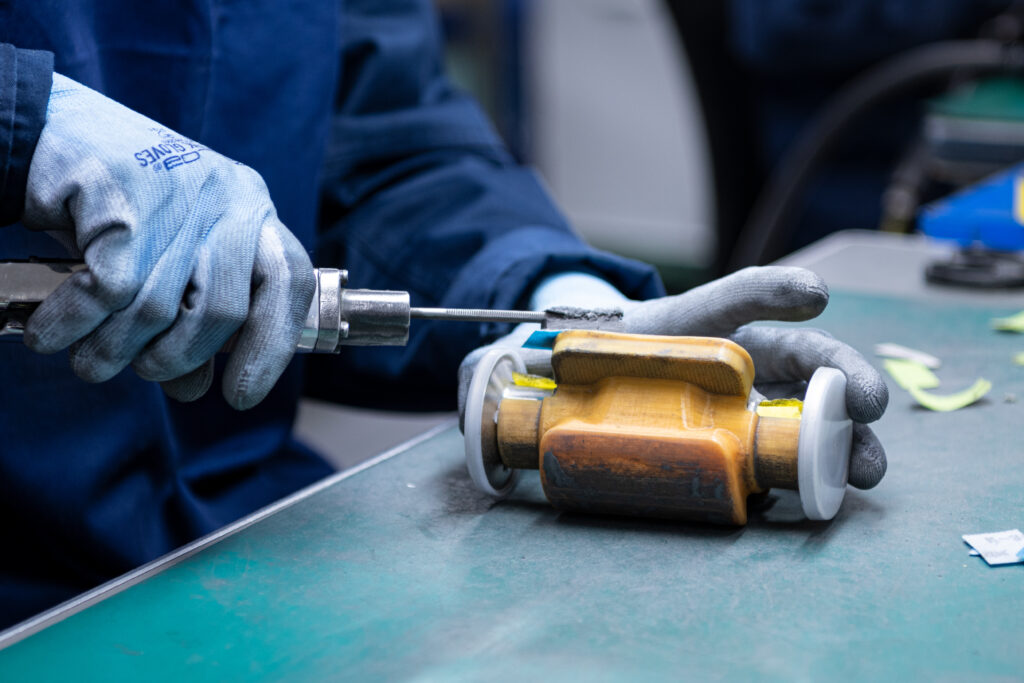
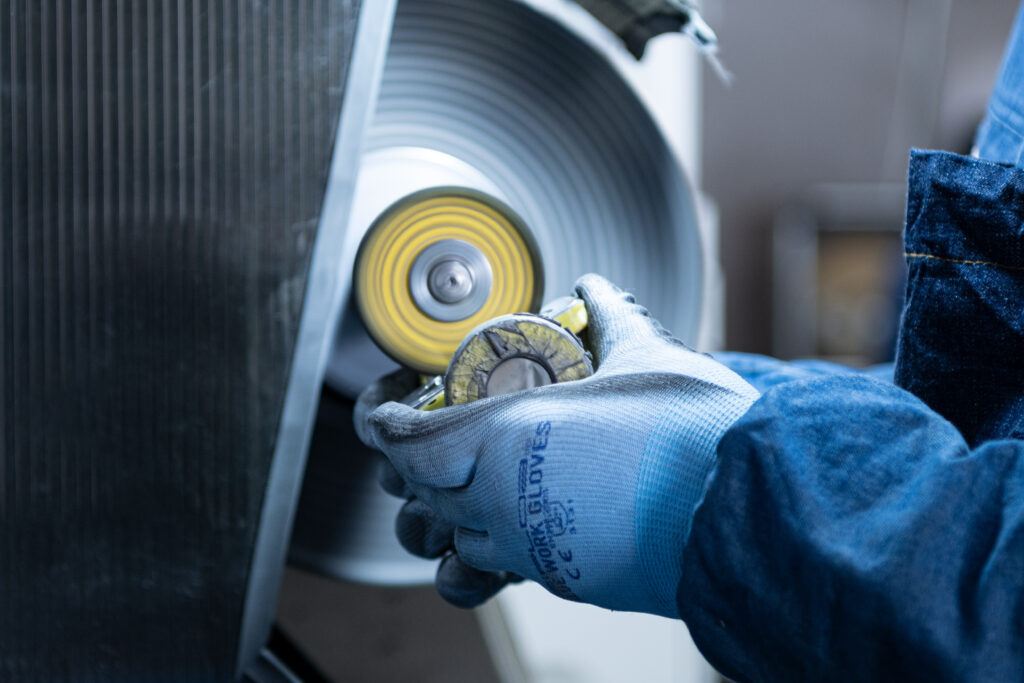
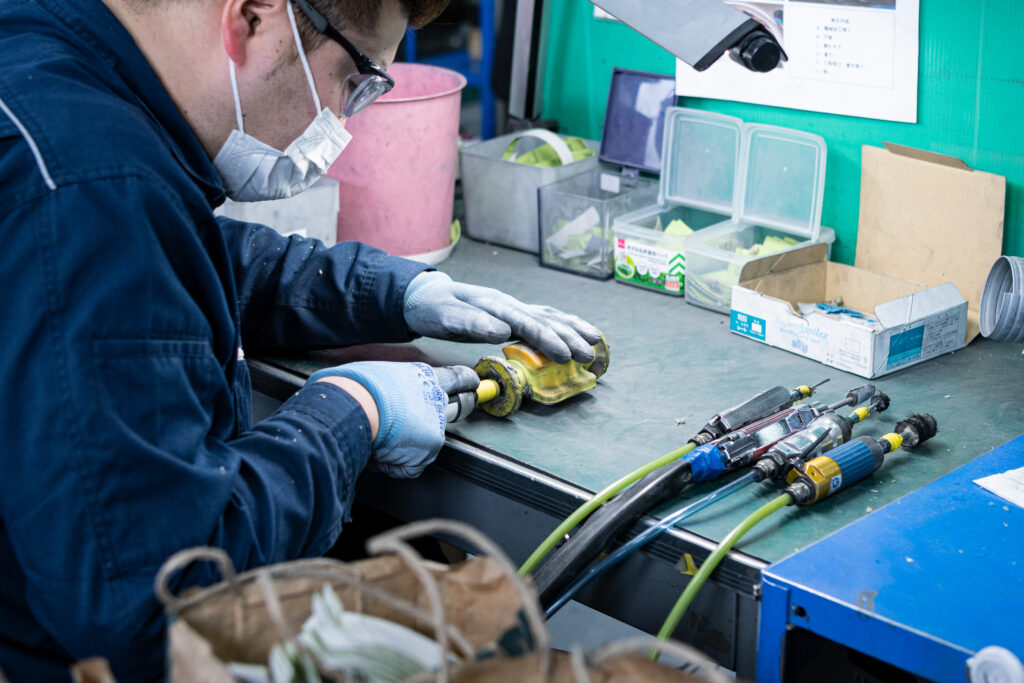
AM製造部品の後加工技術の研究に取り組む
「後加工トライアル(現・AM実用化プロジェクト)※3に参加し、AM造形機(産業用3Dプリンター)で64チタン製のタービンブレードを模したモデルを造形してもらい、加工実験にとりくみました。技術展示会などに加工したサンプルを持っていくと皆さんとても驚いてくれて、新しい仕事につながっています。AM製造部品の研磨技術はこれからも研究を進めていきたいです。」(沼倉氏)
同社では沼倉氏を中心に、センターで運営しているみやぎデジタルエンジニアリングセンターの事業の一つ、後加工トライアルに参加し、AM造形機で作られた複雑な形状を研磨する技術の研究に取り組んできました。現在も、同事業を活用して様々な形状のサンプルピースを作成し、DfAM※4のための後加工技術の研究を行っています。
この研究で得た知見は宮城AM研究会※5で積極的に発表し、AM技術の発展にも貢献しています。
※3 後加工トライアル(現・AM実用化プロジェクト):AM技術を活用した製品や部品の実用化のために、開発に必要なAM造形品をみやぎデジタルエンジニアリングセンターから提供する事業。
※4 DfAM:Design for Additive Manufacturingの略。AM造形の特性を活かす設計手法のこと。
※5 宮城AM研究会:みやぎデジタルエンジニアリングセンターが運営するAM技術と活用方法を学ぶための研究会。同社は宮城AM研究会の運営委員会委員も務めている。
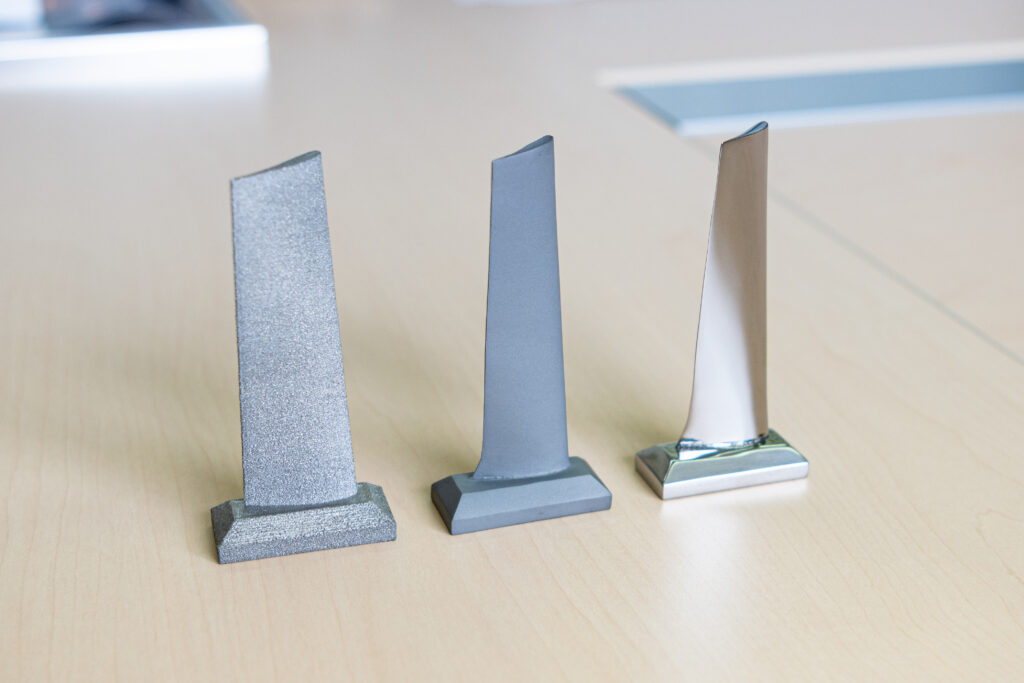
航空宇宙分野の仕事に取り組む若手職員たち
「防衛省向けの中空製品(熱を逃がすために内部が中空状に作られた部品)を担当しています。もっと上のレベルにいきたい。具体的には作業の効率化と高品質な仕上がりを両立できるようになりたいです。」(梶原氏)
「私は防衛省向けのタービンブレードの担当です。宇宙(天体)に興味があったので、求人のとき、航空宇宙分野という言葉に惹かれて入社しました。難しい作業もありますが、先輩に聞きながら技術を学んでいます。これからもレベルアップしたいです。」(今野氏)
「私も航空宇宙分野に惹かれて入社を決めました。普段の仕事では、わからないことはすぐに人に聞くように心がけています。難易度の高い中空製品の加工にもチャレンジしていきたいです。」(横地氏)
「みんなプロフェッショナルな意識を持ってくれていて、互いに技術では負けたくない、もっと技術を高めたいという気持ちで仕事に取り組んでくれています。かといってギスギスした空気も無く、とても良い雰囲気なんです。次はボーイング777Xのエンジン部品加工に取り組みたいとみんなで話しています。」(津田氏)
航空宇宙分野での業務拡大を進めている同社では、積極的に地元・石巻の若手社員の採用を進めています。難しい作業を求められる業務が多いのですが、年齢が近い社員が新入社員をマンツーマンでサポートする体制や、写真入り手順書を使って短時間で技術習得できる仕組みを整えているとのことです。
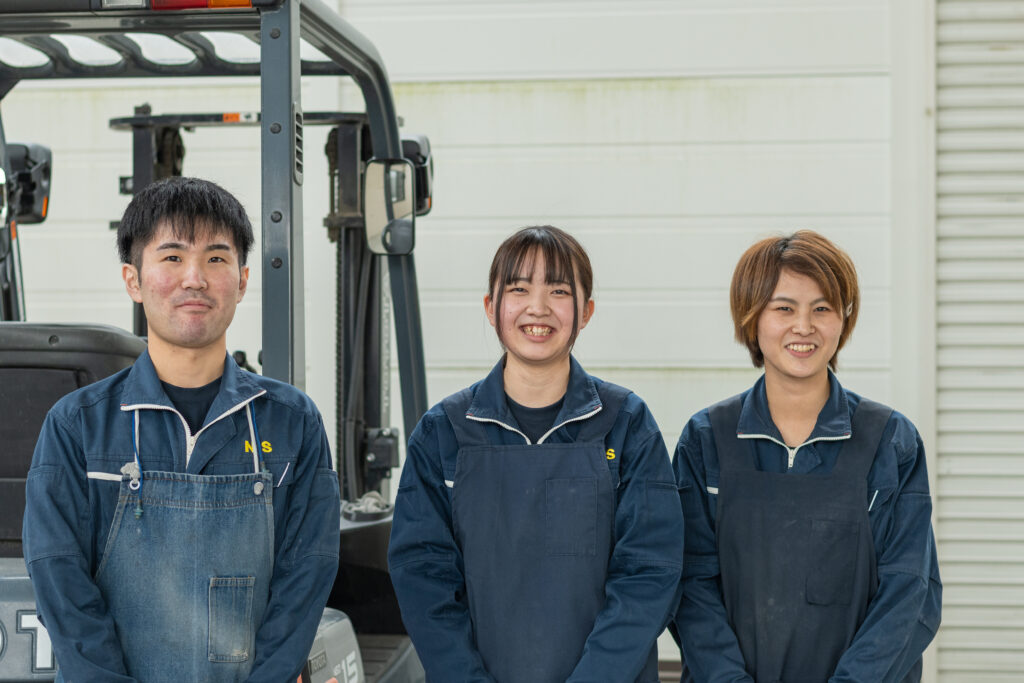
「以前は、それこそ“目で見て覚える”という古い体制だったんです(笑)。航空宇宙分野の部品は一個何十万円もするような部品ばかりで、失敗したときのリスクが大きい。外部アドバイザーの声を聞きながら、作業の見える化、4S(整理、整頓、清掃、清潔)、QCD(品質・コスト・納期)の管理、作業者毎の技能一覧表の作成などをひとつひとつ進め、社員全体のレベルアップに取り組みました。はじめ、作業の手順書は私や沼倉が作っていたのですが、ある社員が“私がつくります”と言ってくれて、今では現場に任せています。現場で作るからこそ、大事なポイントが盛り込まれた実践的な手順書になっているんだと思います。」(高橋氏)
こういった品質向上・品質管理の取り組みを日々積み重ねる同社では、思わぬ良いことがあったそうです。
「航空宇宙分野へ進出するためにISO9001※6を取得したのですが、意外にすんなり取れました(笑)。取得のためにいろいろ調べてみると、ほとんど普段やっていることばかりだったからです。もちろんISOは認証取得よりも運用し続けていくことのほうが難しい。これからも気を抜かないようにしたいです。」(高橋氏)
※6 ISO9001:品質マネジメントに関する国際規格。
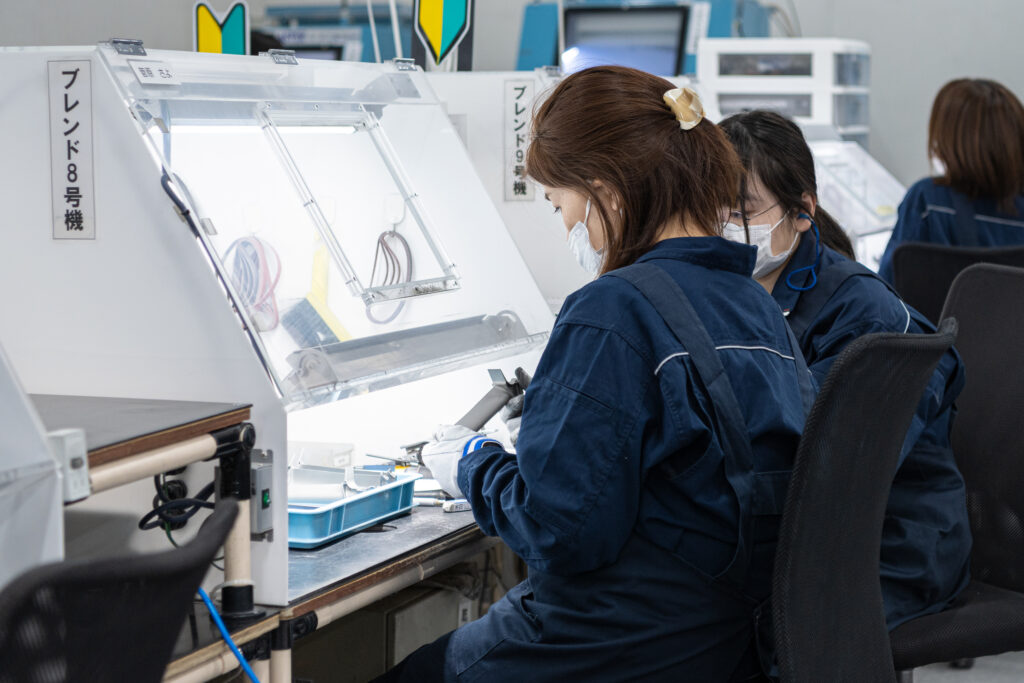
今後のビジョンについて
「今年11月に新建屋が完成予定です。主力の航空宇宙分野の事業を拡充していきます。」(阿部氏)
「AIやIoT技術を活用して、少人化・半自動化を進めたいです。まずはAIで外観検査を行う仕組みをつくりたいですね。IoT分野では(研磨用機器の動力源である)大型コンプレッサーの監視システムや、研磨ツールのモーターにかかる負荷を監視して適切なメンテナンスができるようにしたいです。センターの太田さん※7にいろいろ相談しているんです。」(高橋氏)
業務を拡充しながらも、高品質なものづくり体制を維持していくために、AIやIoTの積極的な活用を目指す同社では、センターの”身の丈”IoT等活用支援事業を利用して調査・検討を進めています。今後は、自動化できる部分はAIやロボットに任せて、人の手でしかできない得意分野を伸ばしていきたいとのことでした。
※7 センター機械電子情報技術部でAIやIoTを担当する職員。
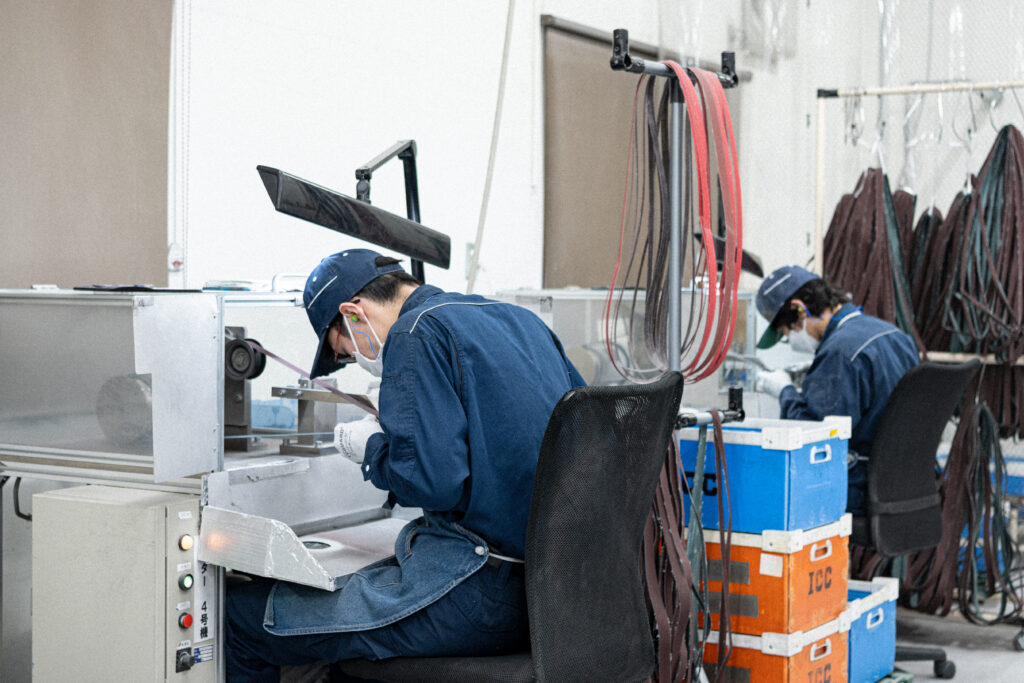
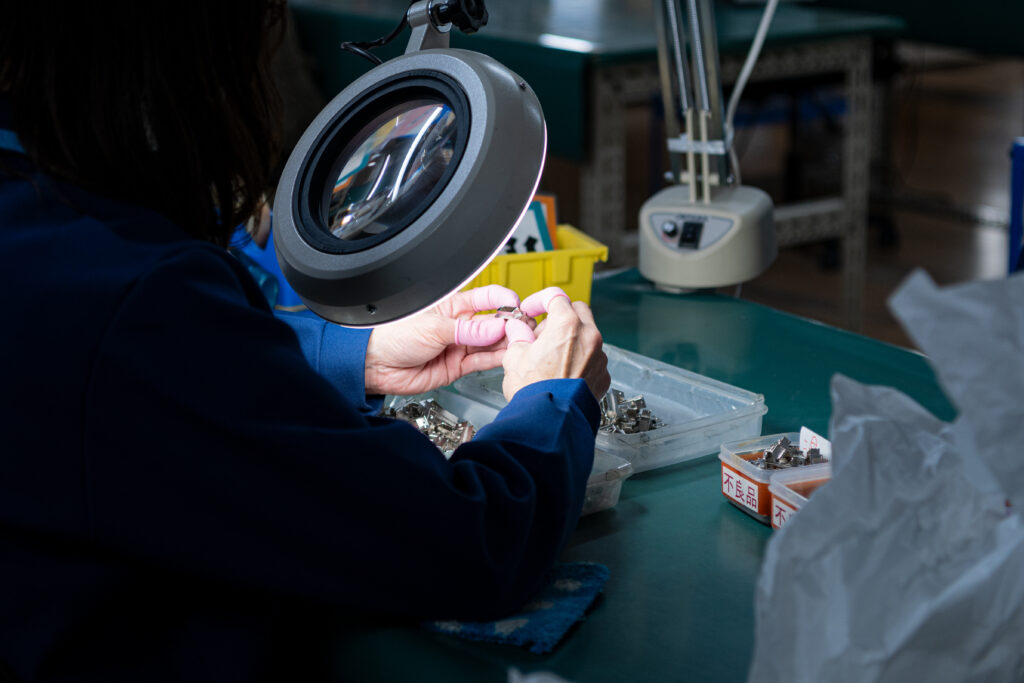
産業技術総合センターに期待すること
「今もチャンレジしたいことがたくさんあります。補助金も含めてチャレンジを応援してくれる体制を作り続けてほしいです。」(阿部氏)
「3D-CADを使える人材の育成に協力してほしいです。自社で治具や機械など、いろいろ自分たちで設計したいですね。」(津田氏)
「精密測定の分野で相談にのってください。(研磨の結果が具体的に数値で示されるため)作業者のモチベーションアップにもつながりますよね。」(高橋氏)
「3Dプリンターで造形した部品の研磨加工技術を一緒になって研究していきたいです。宮城AM研究会にも期待しています。」(沼倉氏)
その特殊な技術力が高く評価され、航空宇宙分野で活躍している同社ですが、今も常に新たなニーズを開拓し、3DプリンターやAIなどの新技術の活用を進める挑戦的な姿勢を強く感じられる取材となりました。
注:秘密保持のため一部画像を加工しています。
会社概要
所在地 | 〒987-1102 宮城県石巻市和渕字日照131番地 |
連絡先 | 問い合わせフォーム:https://ns-kiki.com/?page_id=10 TEL:0225-72-4037 (受付時間8:00~17:00/土日休業) |
ウェブサイト | https://ns-kiki.com/ |
事業内容 | 航空・宇宙部品の研磨加工 医療機器関連部品の仕上げ加工(金属積層造形ほか) 金属製品の表面バフ研磨及び鏡面研磨 樹脂製品のバリ処理・外観検査 輸出入品の電子機器部品の外観検査 電材品等の卸販売 |